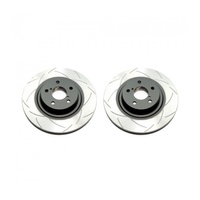
Street Series 2x T2 Slotted Front Rotors (WRX/STi 99-07/09-1
$282.98
$358.20
If you're looking for something in particular, we can help. Drop us a line using the button below.
Submit A RequestShop now. Pay Later. Interest Free.
Make 4 interest-free payments of $114.97 fortnightly and receive your order now. More info
Enjoy Now, Pay Later
Power Slot® rotors are 1-piece, slotted, direct replacement discs for your factory brake system and stock calipers. They offer improved cooling as well as other advantages the competition doesn't offer.
Launched in 1998, Power Slot® was the first premium slotted replacement rotor program in North America. Innovations include e-coating, double-disc grinding, full machining, mill balancing and center-split castings, as well as the availability of directional vanes, cryogenic treatment and the use of Power Alloy. Today, Power Slot® covers more than 2500 applications, all machined in Power Slot's® California manufacturing center. Every Power Slot® rotor is a direct replacement for a factory brake rotor, allowing the retention of factory calipers in the system.
Power Slot® rotors feature a signature "short slot" design. The slot improves brake system performance by wiping away the debris of used friction material that otherwise accumulates between the rotor and pad. This keeps fresh pad material exposed to the rotor surface and helps prevent pad glazing. The edges sweeping the pad slightly increase the effective coefficient of friction, or “bite,” amplifying brake system response to pedal input. By providing an escape path for water, slotted rotors can also improve initial brake response under wet conditions.
E-Coated Finish
Every Power Slot® rotor is finished with a black e-coating on both sides of the hat, inside the cooling vanes and on the outside edge. E-coating is a superior electro-statically applied finish designed to withstand 400 hours of salt water exposure without rusting. This is especially important on both mounting faces of the hat where it touches the hub flange and back face of the wheel. Any accumulation of rust in these areas can lead to installed lateral runout issues.
Double Disc Ground
Power Slot® rotors feature a double disc ground, taper free finish. Double disc grinding ensures parallelism, eliminates run out and provides near perfect disc thickness variation (DTV). Double disc grinding leaves a non-directional finish on the friction surface area for more effective pad and rotor break-in. This special finish also provides quieter and smoother stops.
Machined Finishes
Power Slot® rotors feature 100 percent fully machined finishes including rotor hats. This extra process provides better rotor balance and creates a cleaner, more finished looking component.
Mill Balancing
Power Slot® brake rotors are mill balanced to a tolerance of less than 2 oz-inch. This additional machining operation reduces feedback associated with rotor vibration and provides a smooth, confident application of braking force.
Split Castings
Center-split core castings provide proper heat transfer and thermal efficiency, resulting in superior braking power and safety.
Directional Vane Design
Most Power Slot® rotors match the original factory cooling vane design. In the most popular sports car and light truck applications, Power Slot® has improved the design by using directional (left- and right-handed) vanes to improve cooling. This represents a distinct upgrade from the original equipment rotors, which usually feature a straight vane or pillar vane design. The directional vane is a more efficient air pump. The resulting increase in airflow translates into greater resistance to brake fade and faster recovery from temperature spikes generated by aggressive braking manoeuvre's.
Power Slot® rotors are 1-piece, slotted, direct replacement discs for your factory brake system and stock calipers. They offer improved cooling as well as other advantages the competition doesn't offer.
Launched in 1998, Power Slot® was the first premium slotted replacement rotor program in North America. Innovations include e-coating, double-disc grinding, full machining, mill balancing and center-split castings, as well as the availability of directional vanes, cryogenic treatment and the use of Power Alloy. Today, Power Slot® covers more than 2500 applications, all machined in Power Slot's® California manufacturing center. Every Power Slot® rotor is a direct replacement for a factory brake rotor, allowing the retention of factory calipers in the system.
Power Slot® rotors feature a signature "short slot" design. The slot improves brake system performance by wiping away the debris of used friction material that otherwise accumulates between the rotor and pad. This keeps fresh pad material exposed to the rotor surface and helps prevent pad glazing. The edges sweeping the pad slightly increase the effective coefficient of friction, or “bite,” amplifying brake system response to pedal input. By providing an escape path for water, slotted rotors can also improve initial brake response under wet conditions.
E-Coated Finish
Every Power Slot® rotor is finished with a black e-coating on both sides of the hat, inside the cooling vanes and on the outside edge. E-coating is a superior electro-statically applied finish designed to withstand 400 hours of salt water exposure without rusting. This is especially important on both mounting faces of the hat where it touches the hub flange and back face of the wheel. Any accumulation of rust in these areas can lead to installed lateral runout issues.
Double Disc Ground
Power Slot® rotors feature a double disc ground, taper free finish. Double disc grinding ensures parallelism, eliminates run out and provides near perfect disc thickness variation (DTV). Double disc grinding leaves a non-directional finish on the friction surface area for more effective pad and rotor break-in. This special finish also provides quieter and smoother stops.
Machined Finishes
Power Slot® rotors feature 100 percent fully machined finishes including rotor hats. This extra process provides better rotor balance and creates a cleaner, more finished looking component.
Mill Balancing
Power Slot® brake rotors are mill balanced to a tolerance of less than 2 oz-inch. This additional machining operation reduces feedback associated with rotor vibration and provides a smooth, confident application of braking force.
Split Castings
Center-split core castings provide proper heat transfer and thermal efficiency, resulting in superior braking power and safety.
Directional Vane Design
Most Power Slot® rotors match the original factory cooling vane design. In the most popular sports car and light truck applications, Power Slot® has improved the design by using directional (left- and right-handed) vanes to improve cooling. This represents a distinct upgrade from the original equipment rotors, which usually feature a straight vane or pillar vane design. The directional vane is a more efficient air pump. The resulting increase in airflow translates into greater resistance to brake fade and faster recovery from temperature spikes generated by aggressive braking manoeuvre's.
Street Series 2x T2 Slotted Front Rotors (WRX/STi 99-07/09-1
$282.98
$358.20
Street Series 2x T2 Slotted Rear Rotors (WRX 01-07/Forester
$282.98
$358.20
Street Series 2x T2 Slotted Solid Rear Rotors (WRX 08-18/FXT
$282.98
$358.20
Street Series 2x T2 Slotted Front Rotors (STi 02-20/LGT STi
$404.80
$512.40
Clubspec 4000 2x T3 Slotted Front Rotors (WRX/STi 99-07/09-1
$439.54
$556.38